Operation Time Research Software in Malaysia: Functions, Use Cases, and Industry Relevance (2025)
Operation time research software in Malaysia is increasingly adopted by manufacturers, logistics providers, and service organisations aiming to improve efficiency, identify bottlenecks, and optimise workforce performance. These digital tools allow businesses to analyse, document, and standardise the time taken to complete operational tasks—often replacing traditional stopwatch and clipboard methods.
This article provides a detailed look at how operation time research software is used in Malaysia, its benefits, deployment considerations, and adoption trends across industries.
What Is Operation Time Research Software?
Operation time research software, also known as work measurement or time study software is used to systematically capture and analyse the time taken to perform specific tasks or processes. It allows for the:
- Recording of activity durations
- Segmentation of tasks into elements
- Calculation of standard times (with allowances)
- Visualisation of workflow inefficiencies
- Creation of time-based work standards and productivity benchmarks
These tools often include mobile apps, cloud dashboards, and integration with manufacturing execution systems (MES) or enterprise resource planning (ERP) systems.
In Malaysia, such software is commonly used in lean manufacturing, industrial engineering, and operations improvement projects.
Common Applications in Malaysian Industries
Operation time research software is widely adopted across multiple sectors in Malaysia to improve productivity, standardise workflows, and support data-driven decision-making. Its versatility makes it valuable in both industrial and service-based environments.
Manufacturing and Assembly Lines
Time study software is used on production floors to analyse work cycles, identify bottlenecks, and create standard operating procedures (SOPs). This supports continuous improvement under Kaizen or Six Sigma initiatives.
Warehouse and Logistics Operations
Companies use operation time software to evaluate picking, packing, inventory movement, and loading processes. It helps benchmark performance and develop labour standards for 3PL and e-commerce fulfilment centres.
Food & Beverage Processing
In F&B plants, operation timing tools are used to optimise line balancing, changeover times, and manual processes—critical for maintaining throughput in high-volume production.
Maintenance and Field Service
Utilities and engineering services record and analyse time spent on site visits, inspections, and repairs. This data supports workforce planning and resource allocation.
Healthcare and Hospitality
Hospitals and hotels apply time study methods to non-clinical or operational activities such as cleaning, laundry, and patient transport—improving service efficiency and cost allocation.
Key Features of Operation Time Research Software
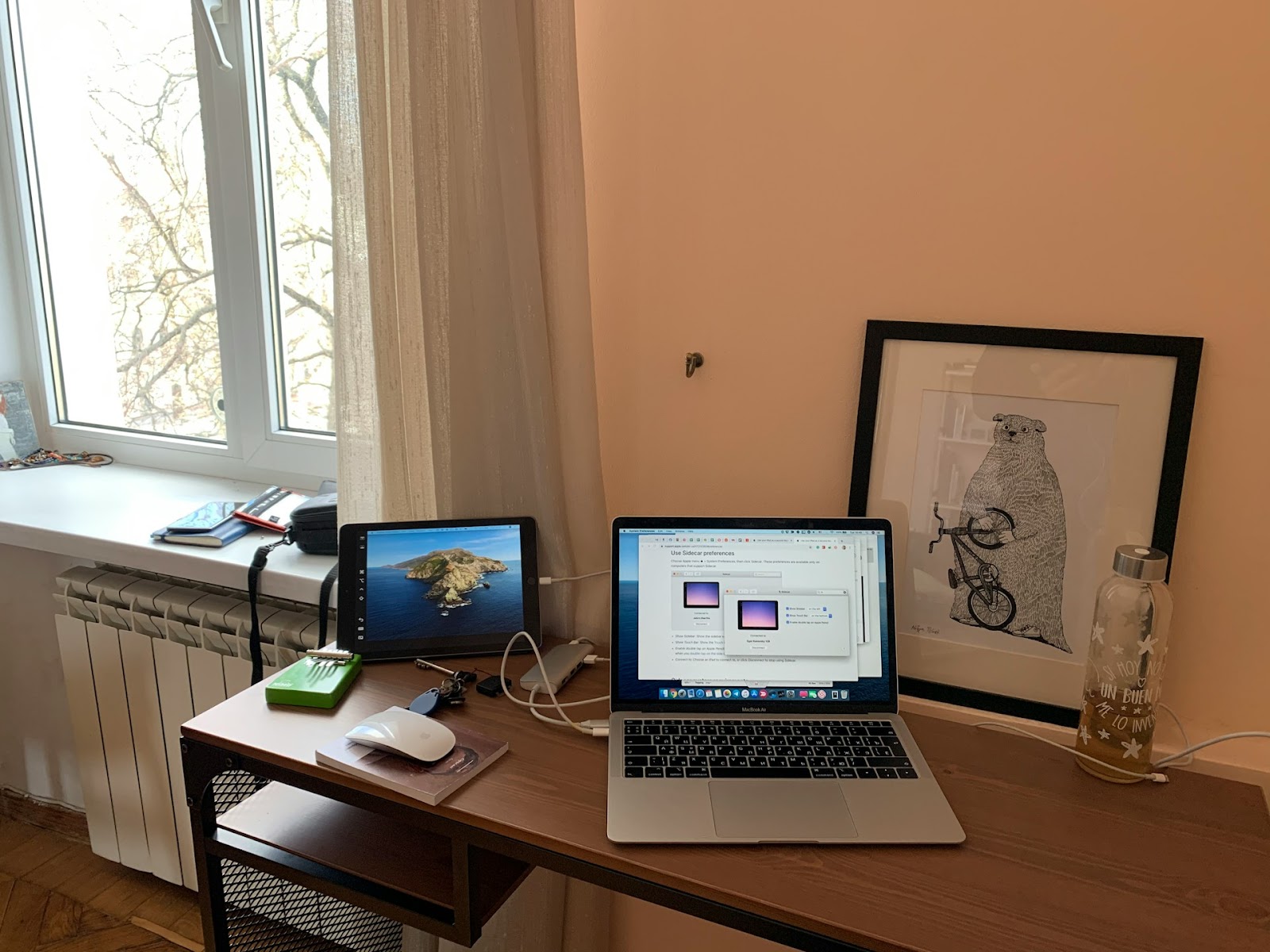
Modern time study platforms used in Malaysia typically include the following functionalities:
- Mobile Time Capture: Allows engineers or supervisors to record task durations using tablets or smartphones in real-time.
- Video Analysis Integration: Enables time analysis via pre-recorded footage for review or training purposes.
- Standard Time Calculation: Automatically factors in allowances for fatigue, delay, and contingencies based on pre-set formulas.
- Data Visualisation: Generates charts and dashboards that display cycle times, operator efficiency, and performance trends.
- Template and Form Libraries: Users can deploy industry-specific study formats for faster setup and documentation.
- Export and Reporting: Creates shareable reports for audits, management reviews, or SOP documentation.
Benefits of Using Time Research Software in Malaysia
Companies adopting time research software report several measurable benefits:
- Improved Operational Transparency: Identifies how long tasks actually take versus expected times.
- Labour Cost Control: Provides data to support manpower planning and productivity-linked compensation.
- Faster SOP Development: Enables quicker creation of standard work documents based on actual observations.
- Lean Implementation: Supports waste reduction by visualising inefficiencies, movement, and idle time.
- Better Cross-Site Benchmarking: Allows companies with multiple facilities (e.g., in Selangor, Johor, and Penang) to compare process efficiency.
Selecting a Software Provider in Malaysia
Okaya works with engineers and factory improvement teams deploying digital tools across Malaysia’s manufacturing sector. When choosing an operation time research software platform, Malaysian businesses should consider:
- Local Support and Training: On-site setup assistance, training for industrial engineers, and after-sales support improve adoption.
- Mobile Device Compatibility: Ensure the software runs on Android or iOS devices commonly used in-field.
- Offline Data Capture: Essential for facilities with poor Wi-Fi coverage or remote locations.
- Customisable Allowances: Systems should allow for user-defined allowances based on Malaysian standards or internal company policies.
- Data Security: Especially for manufacturers working with sensitive client processes or regulated sectors.
Challenges in Implementation
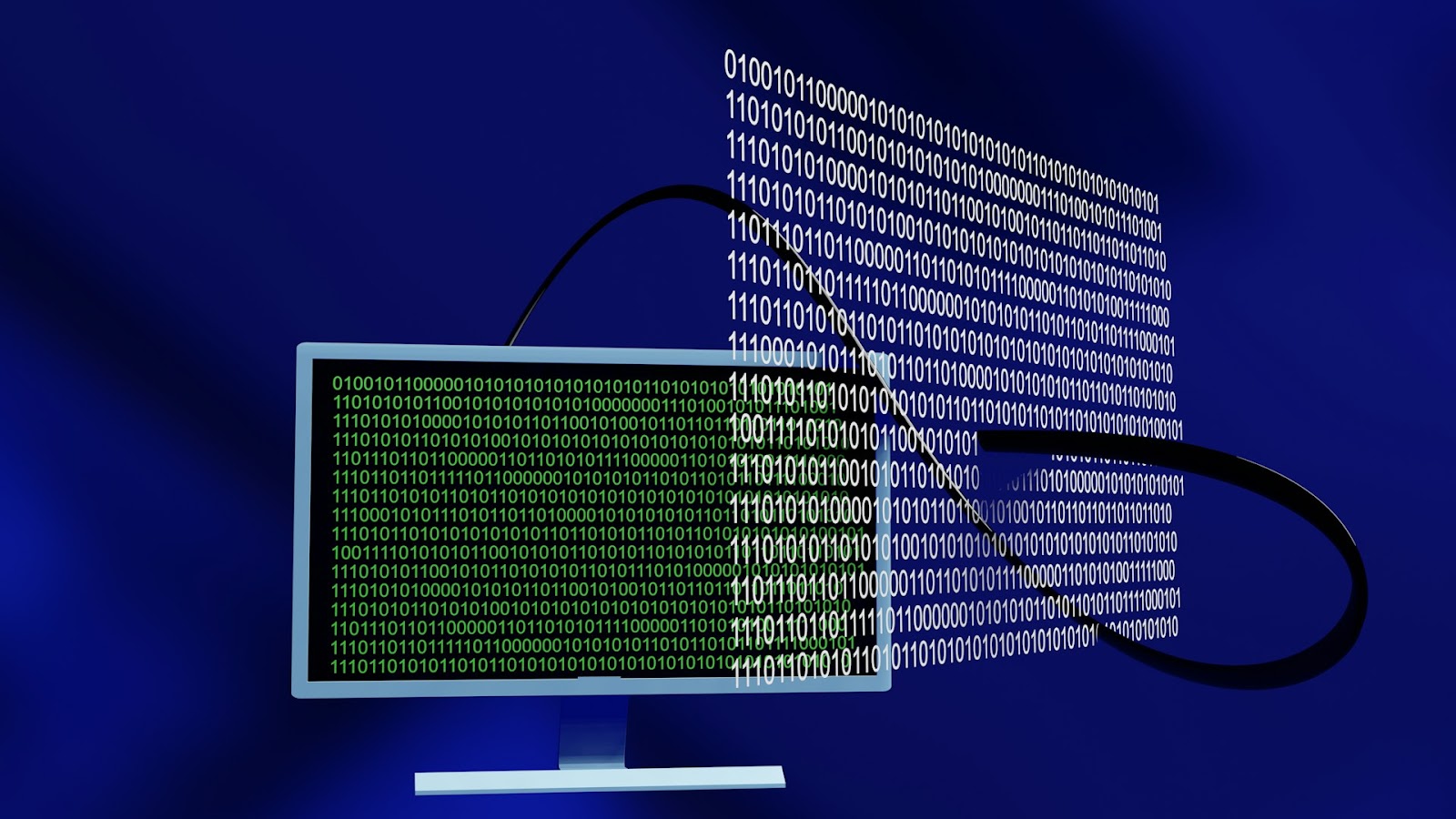
Despite clear benefits, some businesses face challenges when adopting time study software:
- Change Management: Operators may perceive time studies as intrusive if not properly explained and introduced.
- Data Overload: Without proper analysis, raw timing data can overwhelm teams and lead to indecision.
- Inconsistent Use: Time study software is only effective when consistently applied by trained personnel following standardised methods.
- Compatibility with Existing Systems: Ensuring integration with ERP, MES, or HR platforms may require custom development.
Market Trends and Outlook (2025–2030)
Operation time research tools are expected to see increased adoption in Malaysia due to growing interest in data-driven operations, labour optimisation, and digital transformation.
Key Drivers:
- Labour Cost Pressures: Rising minimum wages and a constrained talent pool are prompting companies to study and optimise resource usage.
- ESG and Sustainability Goals: Efficiency gains from lean operations contribute to reduced energy use and resource waste.
- Smart Manufacturing: Industry 4.0 adoption plans encourage integration of digital tools for continuous improvement.
- Remote Audits and Compliance: Time-stamped digital logs simplify external audits and internal compliance monitoring.
Frequently Asked Questions
1. What is operation time research software used for?
It is used to measure, analyse, and optimise the time taken to complete operational tasks, helping improve productivity, standardisation, and cost control.
2. Is this software suitable for SMEs in Malaysia?
Yes. Many platforms offer scalable pricing, making them accessible to SMEs in manufacturing, logistics, and services.
3. Can the software work offline?
Yes. Leading platforms allow offline data entry on mobile devices, with syncing enabled once connectivity is restored.
4. Where can I find a reliable time study software solution in Malaysia?
Software vendors, industrial consultants, and solution partners typically offer deployment services. While Okaya Malaysia Sdn Bhd does not develop software, it supports clients working with such platforms by supplying automation hardware and engineering solutions.
Operation Time Research Software Malaysia
Operation time research software is a key enabler of productivity improvement in Malaysia’s industrial and service sectors. By digitising the traditional time study process, businesses gain actionable insights into workflow efficiency, labour usage, and process standardisation.
Whether applied in production lines, logistics operations, or field services, these tools support data-informed decision-making and continuous improvement. Companies seeking to modernise operations can benefit from collaborating with experienced suppliers like Okaya Malaysia Sdn Bhd, who support the broader ecosystem of digital transformation in Malaysia’s manufacturing landscape.